What Does Scada Stand for in Engineering
What is SCADA?
Industrial processes require careful precision and coordination. Real-time data collection gives you insights to maximize efficiency, reduce overhead costs, and streamline operations. But which data? With so many assets to track, gathering the right information can become burdensome.
Many industrial organizations rely on a Supervisory Control and Data Acquisition (SCADA) system. It helps operators access actionable data and manage equipment. SCADA is a powerful control system that is designed to collect, analyze, and visualize data from industrial equipment. Operators can view critical measurements like temperature, vibration, power usage, and levels across industrial equipment.
Using modern SCADA solutions, operators and field supervisors can access actionable data and manage hundreds of assets without visiting every field device. This can translate to significant cost savings.
Our in-depth guide will walk you through the differences between modern and legacy SCADA solutions and explain how SCADA can improve your operations.
Where are SCADA systems used?
Most industrial settings, such as industrial plants, use SCADA applications. They're typically found wherever industrial automation—the use of advanced technology to automate manual tasks—and process control are used. Utility companies leverage SCADA to support the key infrastructure that forms the backbone of safe, healthy communities. It's critical to maintain power grids and water lines to prevent chaotic and costly outages that affect millions of customers.
These organizations deploy SCADA in highly technical environments where scale, safety, and accuracy are top priorities. Water management, oil and gas facilities, and manufacturing plants are the three most common applications of SCADA systems.
-
Water management and water treatment systems: Water companies use modern SCADA to remotely monitor and control pumps, motors, water tanks, and other critical equipment. Insights from the SCADA software help mitigate asset failure and ensure water services are always running smoothly. For example, San Jose Water Company uses Samsara's next-generation SCADA platform to track live operational efficiency, reduce energy costs, and provide reliable service to over 1 million customers.
-
Oil and gas facilities: SCADA gives oilfield and gas managers real-time visibility into assets that are scattered across remote sites. Web-based dashboards allow operators to remotely view and control mission critical activities such as pressure and vibration levels on tanks and pipelines. This at-a-glance data helps prevent unplanned downtime and potentially disastrous leaks or spills.
-
Manufacturing sites: Considered the origin of SCADA, production floors were early adopters of supervisory control and data acquisition stacks in the mid-20th century. Today, manufacturers can use SCADA platforms to minimize downtime, catching potential machinery problems before they escalate.
What are the differences between legacy and modern SCADA solutions?
The primary difference between legacy and modern SCADA solutions lies in their system architecture. Traditional SCADA systems are typically made up of five or more separate hardware and software components. The more deployed devices, the higher your upfront setup and ongoing operating costs are for a legacy SCADA platform. These complex and outdated solutions also require manual firmware updates, which are easy to neglect leading to greater security risk and a higher likelihood of system downtime.
Cloud-based SCADA systems are part of the larger Industrial Internet of Things (IIoT). They offer a consolidated technology stack for easy deployment across your operations—no matter the scale. This simplified SCADA architecture allows for real-time monitoring and alerts, remote visibility, and is easier to install, streamlining deployment.
Traditional SCADA Architecture: Scattered and Costly
Due to their outdated and complicated setup, legacy SCADA systems are expensive to support and upgrade. There are five main elements of a traditional SCADA system:
-
Human Machine Interface (HMI) software for visualization. Within a SCADA system, a human-machine interface is any user interface or dashboard where operators can interact with a machine, system, or device. It's where water operators or technicians can track real-time data on every connected piece of equipment. These user interfaces allow for full remote control of your assets. They are found in both older and modern HMI/SCADA platforms, but traditional HMIs are less robust than their next-generation counterparts and often limit the number of operators who can view critical data. To learn more about HMI, take a look at our detailed guide.
-
Historian software. Historians are responsible for logging and storing asset data. It allows operators to reference historical trends for analysis and reporting by providing a complete picture of their operations. In a traditional SCADA system, historians are usually "local" or on-site, meaning they require separate servers to connect with the SCADA software.
-
Supervisory computers. Supervisory computers, also known as the supervisory system or station, are the core of SCADA systems. These servers and software that gather sensor data and send control commands to connected field devices. The supervisory computer also communicates with the human-machine interfaces in control rooms to visualize real-time data for users. Many supervisory systems run on multiple servers, which all need security and software upgrades. These critical upgrades are often manual and easy to neglect, but without them, SCADA platforms and the operations they support are left vulnerable to security threats.
-
Communication infrastructure. Communication infrastructure enables data transmission between the PLCs, RTUs, and the master SCADA system. Typically, legacy SCADA solutions require additional setup of radio networks or cellular and Wi-Fi modems in order to connect controllers to the SCADA system. This often includes having to purchase a separate cell service plan that's capable of quickly transmitting large amounts of data. Over time, the additional hardware and network requirements of traditional SCADA communication infrastructure can become costly and difficult to maintain.
-
Remote terminal units (RTUs) and programmable logic controllers (PLCs). RTUs and PLCs are the physical devices that both gather telemetry data from your assets and execute control programs written by technicians or integrators. Once RTUs and PLCs receive a command signal from the supervisory system, they relay that information to the asset in question, thereby controlling field equipment through a network of signals. Depending on the PLC, it communicates with the SCADA network via communications protocols for industrial devices like Modbus or EtherNet/IP.
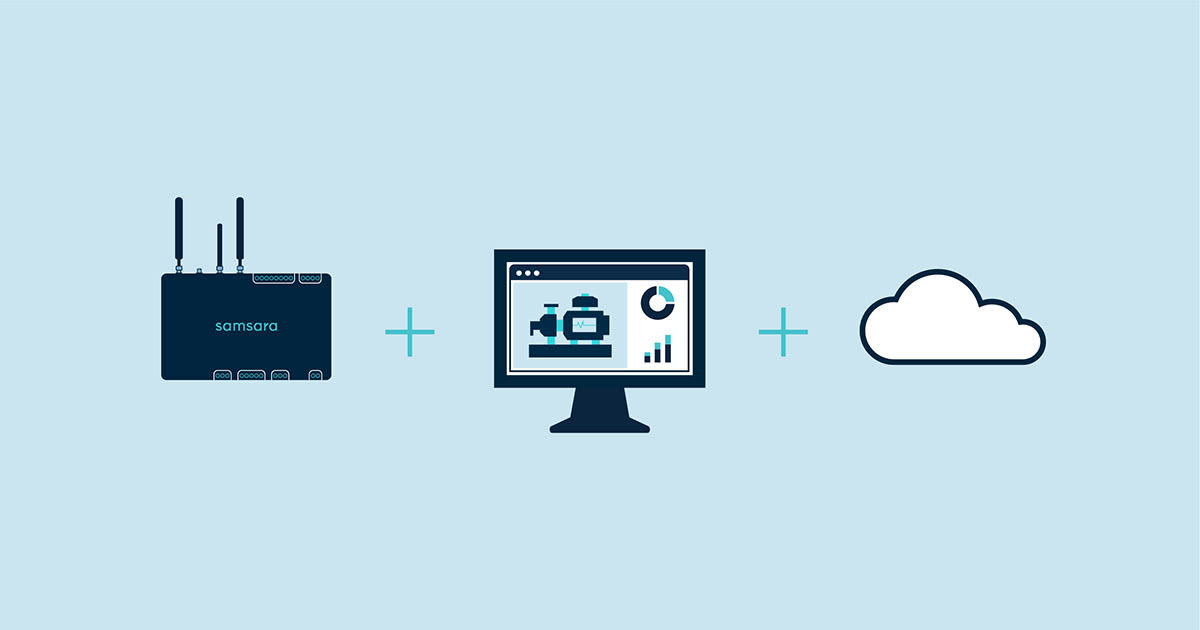
Modern SCADA Architecture: Consolidated and User-Friendly
Compared to legacy SCADA, cloud-based IIoT solutions provide reliable connectivity, unlimited data storage, and powerful insights into every asset. Thanks to the consolidated technology stack of modern SCADA, industrial operations can roll out these advanced systems in a fraction of the time.
Instead of five or more different components to purchase, deploy, integrate, and maintain, a modern SCADA platform makes installation easy with only two main components: hardware and cloud-based software. A typical Samsara SCADA solution includes:
-
A single Industrial Controller that combines gateway and PLC capabilities. Traditional SCADA platforms require you to deploy RTUs or PLCs, modems and self-managed communication networks, and a series of servers to get up and running. Samsara's Industrial Controller eliminates the need for on-premise servers and additional hardware at your sites with cloud-based data storage and management. And with built-in 4G LTE and preprovisioned service, it's easier and faster to deploy in remote environments.
-
Drag-and-drop SCADA software for every user. Operators and multi-site managers require customizable dashboards for their unique use cases. Whether you're controlling valves or monitoring rented equipment, Samsara's cloud-based HMI provides unlimited visibility into asset performance. Our industrial customers are able to view their entire operations, set automatic controls and alarms, access analytics, and print reports from any web browser, including those on smartphones and tablets. Thanks to cloud storage, users can also leverage both real-time and historical trends without the need to deploy separate SCADA servers, historians, and HMI applications.
How do modern SCADA solutions work?
With cloud technology, wireless connectivity, and fewer moving parts, modern SCADA systems make rapid deployment and immediate access to machine data possible.
Once the platform is installed, controllers begin collecting and streaming data from standard 4-20 mA sensors. The controllers can also collect data from legacy PLCs, making it easy to modernize legacy SCADA systems. For example, Woodmen Hills Metropolitan District uses our controllers to gather real-time readings on chlorine levels, flow rates, and pump statuses.
All collected data is then transmitted over a cellular or Wi-Fi network directly to cloud-based HMI dashboards that display machine and environmental data. Here, operators can set start/stop times on equipment, build charts, view historical data, and manage system alarms. And for added peace of mind, onboard storage in the controller allows for offline data logging if a connectivity outage occurs. This data is uploaded to the cloud as soon as connectivity is restored giving you a reliable, uninterrupted view of your operations.
In addition to collecting data, the controllers also initiate commands or signals based on control programs. These programs can be written, deployed, and managed from the cloud, allowing engineers, integrators, and supervisors to make quick changes and adjustments without going on-site.
5 ways modern SCADA improves operational efficiency
Modern SCADA solutions enable operators to track site performance and implement proactive maintenance without the extra cost and energy that traditional SCADA demands. As you think about updating or replacing your current SCADA platform, here are five key benefits of new SCADA to consider:
-
Drive process improvements: A study conducted by market research firm Vason Bourne estimated that unplanned equipment downtime could cost industrial companies as much as $260,000/hour. Unplanned outages affect an infrastructure provider's bottom line and can lead to thousands of unhappy customers. With real-time monitoring, operation managers are able to identify inefficiencies and equipment issues before they cause a service interruption.
-
Shorten response times: With multiple stakeholders and systems that depend on up-and-running operations, it's important to have tools that will resolve asset failure quickly. Most modern SCADA platforms feature smart alarm management that enable your operators to solve issues without the hassle of manual, on-site diagnostics. New HMI screens also provide technicians with unlimited historical trend data to make data-driven decisions fast.
-
Control equipment from anywhere: Traditional SCADA limits both mobility and access to asset data. Whether you're in an office, on the road, or visiting a remote facility, cloud-based SCADA systems give you full visibility and control over your operations. Mobile dashboards allow relevant stakeholders in your organization to assess the current status of your assets and set controls with even fewer on-site visits.
-
Reduce energy costs: According to the EPA, drinking water and wastewater plants often account for 30- 40% of municipal governments' energy consumption. It's no surprise that more utilities companies are prioritizing sustainability. SCADA solutions give you real-time insights into peak energy hours, pump run times, and water flows to help you optimize run times, speeds, and overall asset usage.
-
Streamline compliance and reporting: When managing hundreds of assets, the paperwork piles up in no time. Customizable reports and aggregate data in a single, user-friendly HMI takes the headache out of your reporting process. Equipment as a service companies can also offer their customers the flexibility to print daily reports without manually collecting data.
Industrial customers have used our all-in-one SCADA platform to derive these benefits and more.
Choosing the right SCADA solution for your business
Simplified SCADA platforms help you do more with less. Your SCADA should be flexible enough to meet your unique use case, connect disparate data in one accessible dashboard, and empower all of your key stakeholders with actionable insights.
Samsara offers a complete SCADA solution that can help you scale autonomous operations, so you can focus on providing reliable service to your customers. Reduced labor and maintenance expenses also means added capital for exploring new business opportunities. Our multi-protocol solution enables customers to connect their existing hardware and assets, so you don't have to spend resources on completely replacing your legacy system. Learn how Samsara Industrial can optimize your business and lower operating costs by requesting a free trial today.
What Does Scada Stand for in Engineering
Source: https://www.samsara.com/guides/scada/
0 Response to "What Does Scada Stand for in Engineering"
Post a Comment